Which is better - gas concrete or gas silicate: a
To use gas silicate blocks or gas-concrete in low-rise construction - everyone decides for himself. However, in order for this solution to be weighed, it is worthwhile to carefully study both materials and analyze both their strengths and weaknesses.

Technology Review
Gas and foam concrete in construction
В последние десятилетия при возведении частных домов широко используются пористые материалы на основе бетона. Они производятся по сходным технологиям, и лишь некоторые нюансы изготовления отличают их друг от друга (см.также статью «WITHаморезы по бетону: параметры выбора»).
That is why, before determining whether it is better to use gas silicate or foam concrete, you need to understand the details.
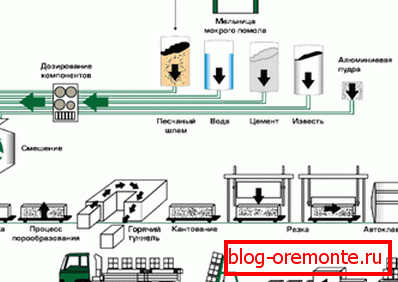
- Foam and aerocrete produced by the same scheme. High-quality cement is used as a raw material, into which special foaming reagents are introduced.
- In the process of "maturation" reagents emit a significant amount of gas bubbles, which are evenly distributed in the thickness of the building block.
Note! Aloe is the claydite, into which is already introduced porous granules of baked clay - claydite.
- Further those nuances about which we spoke above begin. The foam block hardens at a temperature of about 15-250With and atmospheric pressure, because it is very sensitive to the composition of the filler, and to the mode of drying.
- There is often a catch: the low price of the material may indicate problems with curing, and as a result - the low strength of the foam concrete. That is why it is not worth saving, getting the blocks made on "handicraft" technologies.
- Unlike the previous version, the hardening of aerated concrete is carried out in special autoclaves or drying chambers with significant heating. That is why the material is more expensive, but its strength is much higher.
And although the advantages of a gas block in this case are obvious, both materials are actively used in construction. They have good thermal insulation qualities, relatively low mass and low density. The last factor greatly facilitates installation: if cutting reinforced concrete with diamond circles is very laborious, then porous modules can be cut with a special hacksaw with your own hands.

Production and characteristics of silicate blocks
The difference between gas silicate and foam concrete is easy to see if you analyze the manufacturing technology:
- A mixture of cement, sifted sand and lime is used as a raw material.
- In the process of mixing, pore formers are added to the composition, which are responsible for the formation of microscopic cavities in the thickness of the block.
Note! In some brands of material, the instruction also recommends adding aluminum chips, which acts as an activator of gas-forming additives.
- Hardening proceeds in much the same way as silicate bricks: the blanks are fed to an autoclave, where they are processed with high-temperature water vapor under pressure (8–12 atmospheres).

As a result, the answer to the question of whether gas silicate or claydite-concrete (foam concrete, aerated concrete) is better becomes practically obvious. Due to this treatment, building silicate blocks acquire exactly the same properties throughout the volume, which has a positive effect on their performance.
The technology of installation and finishing practically does not differ from the method of using other porous concretes. The products are fairly easy to cut, they are in good contact with both the mortar and the special glue and have acceptable adhesion with plaster and other finishing materials.

Pros and cons
Чтобы определиться, какой материал стоит предпочесть в строительстве, нужно для начала проанализировать сухие цифры, как мы это сделали в таблице ниже (читайте также статью «Бетонолом: как на этом инструменте можно заработать, как его выбрать и на что обращать внимание при покупке»).

Aerated concrete or gas silicate - table of comparative characteristics:
Characteristic | Aerated concrete blocks | Gas silicate blocks |
Material density, kg / m3 | 600-1000 | 450-650 |
Thermal conductivity W / m2*0WITH | 0,15 – 0,39 | 0,11 – 0,16 |
Mechanical strength, kgf / cm2 | 15 - 65 | 25 - 40 |
Frost resistance, freeze-thaw cycles | To 35 | To 35 |
Moisture absorption,% by weight of material | To 16 | Up to 25 |
Masonry thickness with equivalent thermal conductivity, cm | 40 | 30 |
If we consider both materials in more detail, we can draw the following conclusions:
- Blocks gas silicate and foam concrete blocks are desirable to use where the supporting structures do not experience extreme loads, namely in low-rise construction.
- The thermal insulation properties of both materials are quite good, and some lagging of the foam and gas blocks in this parameter can be compensated by additional insulation.
- The high mechanical strength of gas silicate walls is good where it is necessary to ensure maximum bearing capacity with a minimum thickness of the structure.
- The same applies to the mass of the material: a more powerful foundation will be required for a building of aerated concrete modules, which means that its price will be higher.
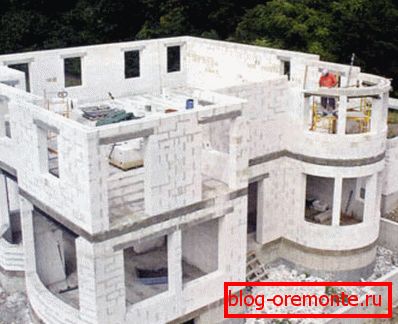
- Equivalent to these materials and frost resistance. However, in the conditions of a variable climate with frequent thaws (and this is practically the entire middle zone of Russia), the gas-block looks more advantageous due to lower water absorption.
Note! The relatively high water-holding capacity of the gas silicate masonry places increased demands on the quality of waterproofing.
- Analyzing the properties of materials, it is also worth noting that both types belong to the category of non-combustible. However, aerated concrete blocks withstand a higher temperature, while the use of products manufactured by silicate technology is allowed when heating is not higher than 4000WITH.
If we talk about the cost, then the foam will occupy the most budget niche. At the same time, gas-blocks and gas-silicate are quite expensive, but they provide savings on additional thermal insulation of the erected structures.
Conclusion
The debate about whether claydite or gas silicate is better is rather unproductive: each material has its own niche of effective use. But it is worth noting that, with the exception of some points (moisture absorption, heat resistance), silicate blocks are superior to other porous concretes.
You will get more detailed information about the technologies and materials used by viewing the video in this article (find out also how to install floor-mounted concrete on the wall).