Monolithic reinforced concrete for ruggedized structures
Unlike block construction, in which prefabricated elements of various shapes and sizes are used, monolithic reinforced concrete is poured into the formwork directly on the object. In this case, the details of the design are holistic, and therefore more durable and durable.
Of course, this technology is quite difficult to implement, but in some cases its use is not only justified, but the only possible one. In the article we will try to describe in detail the methodology for the construction of structures from a concrete monolith, and also give a number of recommendations for the organization of construction works.

Analyzing technology
General characteristics
The technology of construction of buildings from monolithic reinforced concrete is known, perhaps, almost as much as the material itself.
It is characterized by such features:
- All bearing elements of capital construction are erected in place by pouring a liquid solution into the form.
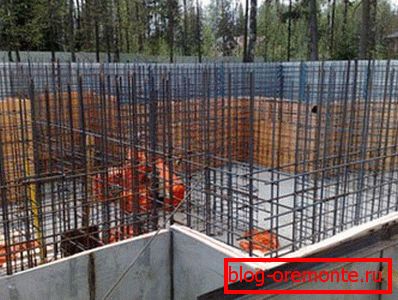
- The configuration of the structure can be arbitrary, and depends only on two parameters: the strength of the frozen concrete and the possibilities for installing the formwork.
- For the mechanical characteristics and the ability to cope with the loads, the internal reinforcement of the structure, which is made immediately before laying, of steel rods of different diameters, is responsible.
- Depending on the volume of the element, the solution can be prepared on site, or ordered separately in production. In the second case, the price increases significantly, but we are able to fill continuously, which drastically improves the quality of the material.

This technology usually produces building foundations. Even when using prefabricated blocks as supports on top of them, experts recommend pouring reinforced concrete monolithic belt with reinforced reinforcement for a more even distribution of loads.
At the same time, this technique can also be used for laying walls, ceilings, arches, etc .: monolithic reinforced concrete houses, bridge supports, tanks and other structures have recently been built very actively.
Key advantages
If we talk about holistic reinforced concrete structures erected by monolithic pouring, then they are characterized by such advantages:
- First, the relatively small number of connecting joints makes the system highly resistant to mechanical stress.. The strength of the bases and walls is ensured by an effective combination of cement mortar and internal multi-contour reinforcement.
Note! A monolithic reinforced concrete house or cottage is much more seismic resistant than a similar structure erected by another technology.
- Secondly, the buildings are characterized by all the advantages that the material of the walls and the foundation provides.: concrete does not burn, does not oxidize, is practically not subject to erosion, etc. With proper operation, the facility can serve from 150 years or more.
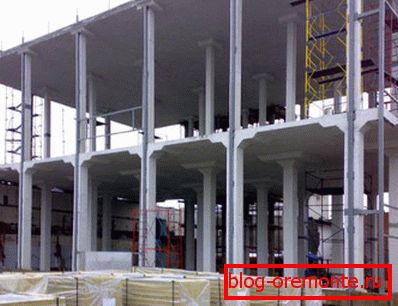
- If we exclude the influence of destructive factors (fires, tremors, vibration, etc.), then over time, the strength of the material increases due to compaction of concrete and more complete hydration of the cement.
- Another group of advantages is directly related to the construction technology: we can give the construction of almost any configurationwithout limiting yourself to the shape and dimensions of the finished blocks.
Of course, it should be noted that pouring concrete walls usually requires the involvement of significant resources, because it is used in the implementation of large-scale projects. At the same time, practically everyone can make a monolithic reinforced concrete garage, and the task will not surpass other technologies too much in terms of labor costs.
Cons and difficulties
Naturally, this construction method is not universal.
Both for him and for buildings erected with its use, such minuses are characteristic:

- Significant weight. It is necessary to lay a powerful foundation for such a structure, since both walls and floors are very heavy. Yes, and not any soil will withstand the load, because without geological surveys can not do.
- The walls themselves are notable for their significant sound and heat conductivity. Almost all residential and public buildings of monolithic reinforced concrete require additional insulation.
- Breathability of the walls, in contrast, is considered to be very low. This leads to a violation of natural air exchange, and therefore, even at the design stage, it is necessary to put in powerful ventilation.
- The strength of the material also has its drawback: the structure after curing is almost impossible to process. For the installation of unplanned communications, diamond drilling of holes in concrete is necessarily required, since conventional drills in most cases only scratch the surface.
Note! Dismantling of such buildings is also very problematic. Even for the demolition of one wall, cutting of reinforced concrete with diamond circles is used, and there are practically no alternatives to this expensive technique.

- As for the construction process itself, the most difficult area is formwork. When a large scale of work, the instruction recommends doing it with a margin of safety, since the destruction of even a small area can permanently stop the pouring process.
- If the construction is erected in the winter period, then concrete heating is required. Taking into account the significant amount of material, the costs can be estimated as very substantial: you will have to spend money on wires and on electricity.
The process of pouring concrete structures
Construction of formwork
Monolithic reinforced concrete tanks, columns, arches, walls and foundations are built approximately in the same technological scheme. Below we describe its main stages.
As we noted above, one of the main advantages of monolithic construction is the possibility of constructing complex architectural forms. Naturally, the design turned out the way we need, you must use the appropriate formwork.

The formwork is a form that limits the spreading of the solution and provides it with support during the setting and initial curing. For the construction of horizontal, vertical, inclined and other elements, different formwork systems are used, the main types of which are described in the table below:
Formwork Type | Features of a design and use |
Collapsible shield | The most simple and common variety. It consists of a set of individual elements (depending on their size, sometimes they produce small-plate and large-panel formwork), connecting blocks and props, which give it rigidity. It is used for concreting structures of typical size, usually it is easy to move and assemble with your own hands or with the use of light construction equipment. |
Volumetric-passive | It includes several U-shaped sections, used for concreting walls and floors with one monolith. Used in multi-storey construction, mounted and dismantled exclusively using a truck crane. |
Block | Variety of volume-formwork formwork. Involved to simultaneously fill several (most often three or four) load-bearing walls without overlapping. Usually used in combination with large-panel, which provides the formation of external surfaces. |
Tunnel | A variation that can move in a horizontal plane. Designed to fill two walls with overlapping above them. With the use of tunnel formwork consisting of two detachable segments, reinforced concrete monolithic domes are usually poured. |
Sliding | It is used in high-rise construction. The form is installed around the perimeter of the structure, and as the concrete is poured, it rises upwards with hydraulic jacks. |
Pneumatic | Enough new variety, which is a strong, but elastic airtight shell. When using the formwork is installed inside the structure, after which the air is forced under pressure. Allows to form complex and curvilinear cavities of relatively small volume. |
Non-removable | After polymerization of concrete becomes part of the structure. Sometimes plays the role of a heat insulator or decorative cladding. |
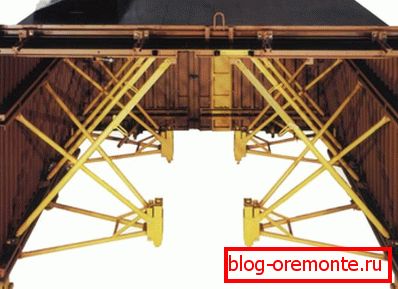
Most of the varieties described above are used in industrial construction. For self-erection of structures apply panel models with a part size of not more than 3m2 and weighing up to 50 kg. On the one hand, the use of such systems increases the rows of work, but on the other - we can do on our own, without involving heavy equipment in the construction.
The process of installation of formwork itself usually does not cause difficulties. If you need a reinforced concrete monolithic slab, then under it dig a pit, along the sides of which install shields. For ground structures, the important point is to strengthen the walls, since a significant mass of the solution can destroy them. Usually saved by the use of thicker shield elements and an increase in the number of props.

Preparation of the solution
When the formwork is selected and installed, it is necessary to prepare the solution.
To fill the monolith applies this ratio:
- Brand cement not lower than M350 - 1 part.
- Sifted sand - 2 parts.
- Filler (gravel from solid rocks) - 3 parts.
- Water.
The amount of liquid in the solution is determined in each case individually. It is best to first mix the dry ingredients to obtain a homogeneous mass, and then gradually add water to the solution, bringing it to the consistency of thick cream.
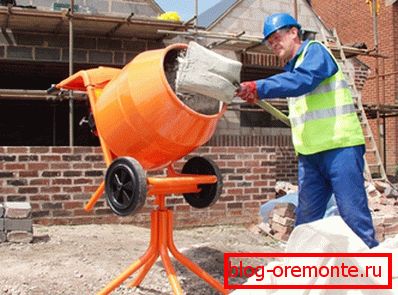
If you want to improve the operational properties of the solution, you can add to it:
- Detergents with anti-fat effect. A teaspoon on a bucket of liquid concrete significantly reduces its shrinkage and increases strength.
- PVA glue. 200 ml per bucket increases flowability, which greatly simplifies the process of pouring complex shapes. In addition, the presence of glue in the solution improves the adhesion between cement and reinforcement.
- Liquid glass. Reduces porosity, accelerates the initial setting, increases the heat resistance.
Note! An excess of liquid glass leads to a very rapid hardening of the material, so you should not use it when pouring large volumes.
As we have said, for private construction it is quite possible to prepare a cement mortar in a concrete mixer. If you are building a large building, it is better to immediately acquire the desired volume and organize its continuous supply to the object.

Reinforcement and coating
In parallel with the preparation of the solution, the structure is reinforced:
- For the manufacture of valves used metal parts of different diameters. So, when forming large bearing elements, rods with a cross section of 15-25 mm can be used, while for ordinary walls, rolled steel up to 10 mm is sufficient.
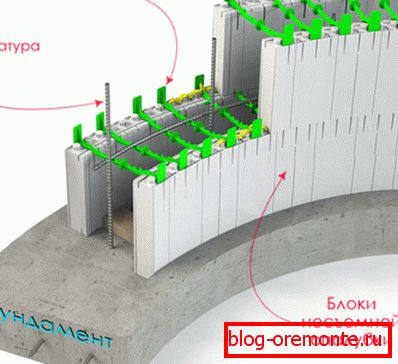
- The reinforcement cage is tied or welded, then lowered into the formwork. In some cases, horizontal mortgages are inserted through special slots in formwork panels.
- The reinforcement is installed in such a way that it is not less than 30-50 mm from the surface of the poured concrete. This is done both to increase the strength of the structure, and to avoid corrosion.
Note! In parallel with the reinforcement is the installation of embedded pipes, which will be communication. Also, if work is carried out in the winter period, a concrete heating system is installed at this stage.
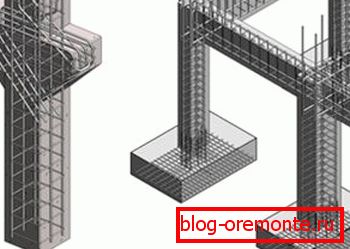
After the reinforcement is completed, the grouting is performed:
- The formwork is filled gradually by feeding the liquid concrete from the gutter.
- To optimize the process, the object is usually divided into tiers (vertical division) and grabs (horizontal). At first, all the grips of one tier are filled, then move on to the next.

- After pouring, the solution is compacted with a vibrating tool.
- Drying of concrete is carried out in such a way as to promote maximum strength. For this, the formwork is covered, which reduces heat loss and reduces the rate of evaporation of water.
- The dismantling of the formwork is carried out only after the design has gained at least 50% of the strength of the value provided for in the project.
Conclusion
Construction of monolithic reinforced concrete cottages, in spite of all its labor intensity, allows solving complex engineering problems. Erected buildings are reliable and durable, but at the same time, they require additional finishing to ensure comfort. In more detail, the techniques used are shown in the video in this article.