Concrete production technology: classification, proportions
According to GOST 25192-2012 and GOST 7473-2010, all concretes are subject to a certain classification according to their purpose, type of binder and aggregate structure, as well as according to the conditions under which they hardened. If we are talking about prefabricated concrete, then it is prepared in the factory, but the mixture for monolithic structures can be prepared at home.
What often do developers in the private sector. Below we consider the main types of such mixtures and methods for their preparation, as well as show you the video in this article on this topic.

Concrete
Binder
Note. Regardless of where the concrete is made - at the factory or at home - the binder is the main factor determining the properties of the mixture. Consequently, the solutions are divided into cement, gypsum, silicate, slag base, polymer special and combined.

- The most popular in our time can be called a mixture based on cement, which are made from, both monolithic and prefabricated concrete structures and structures.. Here, Portland cement is most often used as a binder, but apart from it, pozzolanic and slag portland cement are also used. In addition, this group includes decorative (white and color), non-shrink, alumina and straining cements.
- Gypsum-based concretes are used more as finishing mixtures. (figure molding), but among them gypsum cement is also very popular, which is characterized by high water resistance and elasticity.
- On the basis of latexes and water-soluble resins, polymer cement concretes are mixed together with cement..
- From solutions of ground slag, closed with alkaline solutions, slag-alkaline concretes are made..
- Lime-based autoclave method, rather rarely used silicate concretes are made.
- For the manufacture of special (heat-resistant, acid-resistant) concrete use special binders, such as liquid glass, glass fiber and slag elements. Of course, the price of such mixtures is quite high, however, they are in demand.
Washed concrete

Note. In general, the production technology of washed concrete consists in washing out the top layer of cement-short pastry, that is, the binding component with part of the aggregate opens the aggregate of a larger fraction.
This technology is produced by vibrating or vibratory casting, where the liquid components shrink, exposing the texture of natural stone (pebbles, granite or marble). In this case, only its upper part opens - two thirds of the fractions are absorbed by the solution, and are part of the monolith. For more complex geometries, G-05 gel, C-10 lacquer and P-07 paper are used, which is often applicable to the smooth surfaces of paving slabs, panels and fences.
Such elements can even be made by hand - for this, a form is prepared and a gel is applied on its surface (if the form is collapsible, it is assembled) - all this is done at room temperature. After that, the form is put on a working vibrating table and filled with the mixture. We put on one day the finished part for hardening, and then under the pressure of compressed air and water we blow off the top layer of dough, which has not yet become stronger.
Asphalt

Note. The entire technology for the production of asphalt concrete may differ in purpose and composition. These are all oil construction, roofing and road viscous, which are manufactured according to GOST 6617, 9548 and 2245, respectively.
In most cases, asphalt is used as a pavement and this includes sand, fine crushed stone, mineral powder and, of course, bitumen, which serves as a binding element. Coarse aggregate (crushed stone, gravel), approximately 85% is the bulk of asphalt, but the connecting element, that is, bitumen, is only 6%. At the same time, all components after mixing are subject to rapid laying on the surface to be treated.
Any type of asphalt (sandy, fine-grained and coarse-grained) after preparation is subject to immediate laying (in a hot condition), since otherwise it cannot be tamped to the desired state - the mixture is too fragile. Nevertheless, there are three ways of production - hot, warm and cold.
The difference is that manufacturing takes place at a certain level of temperature, that is, the temperature at which all the components are mixed. If the method of cooking is warm or hot, then all the components are mixed in a hot state, and e with the cold method only one component is heated.
Cement concrete and proportions

By and large, the technology of concrete work depends on the type of the element itself, that is, it can be prefabricated or solid concrete, which, in turn, differs in density class. As mentioned above, concrete could contribute not only to the strength of the building, but also its resistance to all battles, including shelling. For general information, the technologies were developed by professors Malyuta I. G. and Shulyachenko A.R.
If you paid attention to the table, then you saw that the composition of concrete (proportions of components) is very different from each other in the number of components per cubic meter. Of course, in the private sector you can ignore such norms, however, the instruction requires that the composition of the components does not differ from the norms established by GOST 25192-2012 and GOST 7473-2010.

Now let's talk about what is most often used in construction and repair works, that is, how a concrete mortar is prepared - however, we have already mentioned that these can be either prefabricated or monolithic structures. Besides the fact that there are various connecting elements and aggregates, there is also reinforcement of structures, that is, reinforcement.
Standard | The norm for this standard |
FER 06-01-001-17 | 187kg / m3 |
FER 06-01-001-16 | 81kg / m3 |
Number of valves per m2
In general, the amount of reinforcement or steel per cubic meter is determined by weight, the same standards, which were mentioned above, but here you can simply pay attention to the frame device.
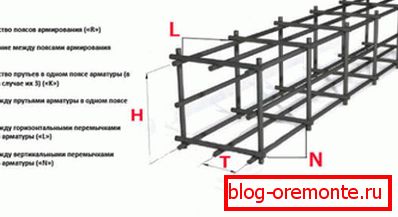
Cement-sand mortars for concreting, in addition to a certain aggregate fraction, also require reinforcement - in fact, such a framework is responsible for the integrity of the structure in general. That is why, before making prefabricated or monolithic elements of concrete, the frame is assembled of reinforcement, which, in fact, is responsible for the entire structure.

In the process of solidification from the mixing water, pores remain, which significantly reduces the density of the concrete solution, therefore, vibrating is performed for precast and monolithic concrete. This process is carried out on vibrating tables (prefabricated structures) and with the help of submersible vibrators with different amplitude of oscillations of the mace.
The amplitude of oscillation of the vibrator is selected in accordance with the size of the aggregate fraction, so the units come in low, medium and high amplitude of oscillation.
- The amplitude of the low-frequency instrument is up to 3500 oscillations per minute and is applicable for a fraction of 3-5 mm;
- mid-frequency - from 3500 to 9000 vibrations per minute for a fraction of 1-1.5 mm;
- high-frequency amplitudes of 10,000–20,000 are used for fine-grained concretes (0.1–1 mm).
Conclusion
In low-rise construction, to which the private sector can be attributed, monolithic concrete is most often used to fill the strip footing and sometimes the basement, as a continuation of the tape. To do this, usually use a mixture of class B20, B22 and B25, corresponding to the brands M250, M300 and M350.