Concrete heating with heating wires: detailed technology
Among the various techniques that are used in laying the foundations and other construction work in the winter period, the important place is occupied by the heating of concrete with the PNS wire. The use of this technology with the observance of all the rules allows you to create optimal conditions for the curing of a hardening cement mortar even if the ambient temperature drops well below zero.
In our article we will describe how to organize such processing, how to choose a wire for heating concrete, and also what you should pay attention to when operating the system.

Overview of techniques
To ensure the correct hardening of the concrete, it is necessary that all the cement in the mortar should react with the water. This process is called hydration, and it breaks down if all or part of the moisture turns into ice.
To avoid this, use different methods:
- First, with a small amount of work you can add components to the solution that prevent freezing. The disadvantage of this technique is the inability of such additives to withstand severe frosts, as well as higher cost of work.
- Secondly, in case of a short-term cooling, you can simply provide high-quality thermal insulation of the poured foundation or another supporting structure. In this case, a formwork made of materials with low thermal conductivity is used, and on top of the concrete is covered with multilayer polyethylene or roofing material.
Note! A variation of this method is the so-called "hot thermos" - before pouring concrete into the formwork, the concrete heats up to 60-700Since then carefully isolated.
- For active heating is often used electrode method. In this case, the conductors are either immersed in the thickness of the solution, or are located on its surface. The electric field formed between the conductive plates or rods, gives a portion of the energy to concrete, maintaining its temperature at a high level.
- However, the most effective and practical method is the use of special heating cables. They are laid in the thickness of the concrete, after which they are connected to a special transformer and heat the material. The price of conductors is relatively small, because this method can be recommended for large volumes.
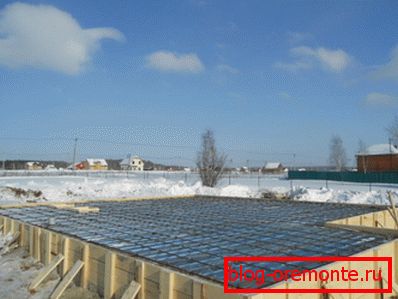
As practice shows, the most effective is the combination of methods of passive heat saving and active heating of concrete. Below we consider the details of this process as detailed as possible.
Cable warming technology
General scheme
When working in temperature conditions, reaching - 400, the wire for heating concrete is almost the only possible option to ensure the hardening of cement.
In this case, the heating process itself is organized in the following way:
- First, the formwork is not mounted on the object.. To reduce heat loss, it is better to make it from insulating materials.
- Then the reinforcement cage is installed in the formwork. Special heating wires are attached to the reinforcement cage.
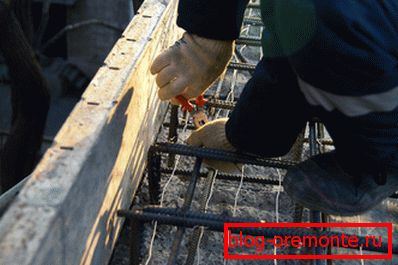
- The lengths of the wires are selected in such a way as to ensure the most uniform load on each section.. All fragments are connected to one conductor bus, which is located outside the formwork.
- Then the solution is poured and compacted.. At the same time, vibration treatment of the cement mass is allowed, since, unlike splicing, it does not damage the conductors.
- Next, the connecting buses are connected to a step-down transformer.. Current is supplied to the system, and the wires gradually heat up, preventing the liquid from freezing in the bulk of the material.
- The operation of the transformer does not stop until the concrete has gained the desired strength.
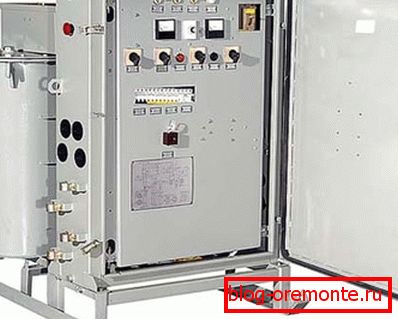
Process physics
What happens at this time in the thickness of the solution?
- With the passage of a current of a given force and voltage, the wire for heating concrete gradually increases its temperature due to considerable resistance.
- Part of the temperature is transferred to the environment, and water does not go into a solid state, while remaining available for cement hydration.
- Also, due to the absence of ice crystals in the thickness of the concrete, pores are not formed, which make the material heterogeneous and reduce its strength.
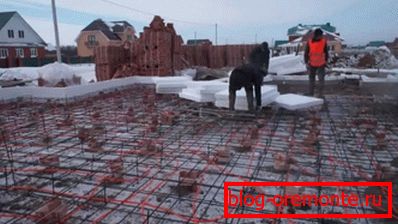
- An additional advantage of such heating is increased reliability of reinforcement: firstly, due to the gradual reduction of available moisture, the risk of reinforcement corrosion decreases, and secondly, the concrete is fixed on the metal frame more evenly.
Note! Cutting reinforced concrete with diamond circles makes it possible to verify the effectiveness of this technique: the material becomes more durable and cannot be processed by other means.
- After reaching concrete certain performance indicators, the heating is stopped. The instruction recommends lowering the temperature gradually, since only in this case can the cracking inside the material be avoided.
Actually, this is exactly what happens in the process itself.
If you decide to organize cable heating of concrete with your own hands, we strongly recommend that you study the following section. Naturally, it must be remembered that in order to perform these works, one should have an appropriate tolerance, so for those who do not have the “crust” of an electrician, the recommendations below will be of an introductory nature.
Methods of work organization
Selection of conductors
Since the heating wire for concrete is the central element of the entire system, it must be chosen very meticulously.
The following considerations are fair here:
- As a main heating conductor, a PNSV wire with a core thickness of 1.2 or 1.4 mm is best suited.
Note! In some cases, namely when heating large structures, it is allowed to install a system from a PNSV cable with a diameter of 2, 2.5 or even 3 mm.
- A steel conductor serving as a current-carrying element can be galvanized - this has a positive effect on the heating efficiency, as well as on the reliability of the system.
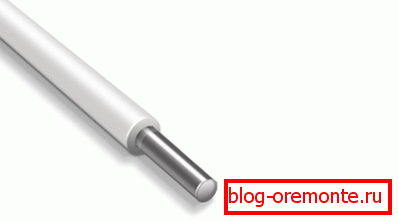
- To ensure effective heat transfer, as well as eliminate the risk of electric shock, the steel core of the PNSV cable should be covered with PVC or polyethylene insulation.
- Do not use a cable with polyethylene protection in reinforced structures: during power surges or prolonged operation with maximum load, there is a risk that the polyethylene will melt and short-circuit the wire to the reinforcement.
- At the same time, polyvinyl chloride at low temperatures (-100C or less) due to a decrease in elasticity becomes brittle, and therefore may crack during the installation phase.
- The consumption of the PNSV 1.2 wire is approximately 50 meters per cubic meter of solution.
When using cables, it must be remembered that the operating current for a conductor located in the thickness of the solution is about 15 Amps. In this case, such a current is excessively large in air, and most often leads to conductor burnout due to insufficiently effective heat dissipation.

To avoid this, the so-called “cold ends” are used to connect the conductors in the concrete with a transformer or a common busbar - wires of a larger cross-section that are less susceptible to temperature loads. As the “cold end”, a meter-long section of the APV-4 cable is usually used, which is connected to the PNSV twist with x / b tape.
Laying scheme
Installation of conductors can be carried out according to one of two schemes.
Below we describe the details of the arrangement of each of them:
- The wire for heating concrete is cut into equal lengths (most often it is 17 or 28 meters) and twisted into spirals with a diameter of about 40 mm, forming the so-called threads. For curling spirals most often used a special machine with electric drive.
- When connecting under the "triangle" all conductors are divided into three equal groups. The wires in the groups are connected to each other in parallel, after which the groups are attached at three points. From each point we connect the cable to the output terminal of the transformer.
- Somewhat differently distributed wire when connecting the "star". Every three threads are joined into one knot, forming a “troika”. All triples are connected to each other, and, as in the first case, we connect to the transformer.
- To understand the topology of these schemes will help the images that are given in this section.
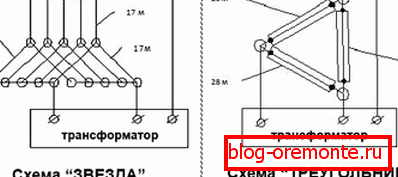
To facilitate the calculation of the wires for the heating of the concrete solution, you can use special calculators. Also, some examples for the most common situations are given in the table below:
Transformer type | PNSV diameter | "Star": the number of triples with a beam of 17 m | "Triangle": the number of groups of threads with a length of 28 m |
SPB-40 | 1,2 | 14 | 3 to 8 |
1,4 | 12 | 3 to 7 | |
SPB-80 | 1,2 | 28 | 3 to 13 |
1,4 | 24 | 3 to 11 | |
SPB-100 | 1,2 | 35 | 3 to 16 |
1,4 | 29 | 3 to 14 | |
380/36 by 6 kW | 1,2 | 5 | 3 to 3 |
380/36 for 2 or 2.5 kW | 1,2 | 5 | 1 (three threads) |
Installation of the heating system
The process of installing the system itself is quite simple:
- First we build the formwork and lay the reinforcement cage in it. Tips for arranging formwork are given above.
- Then we cut the PNSV cable in accordance with the required volumes and form spirals for heating from it.
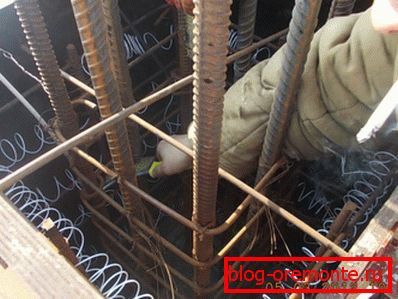
- Next, we lay the cable in such a way that the distance between adjacent conductors is at least 15 cm.
- When forming the bend, we make sure that the conductors do not break, and the integrity of the insulating layer is not disturbed. The recommended bend radius is at least 25 mm.
- We attach the wires to the reinforcement cage in such a way as to avoid their displacement during pouring and vibration compaction of the solution.

- Conclusionные концы соединяем в группы в соответствии с выбранной схемой монтажа (см. выше). Зачищаем края проводников и присоединяем их к «холодным концам» путем скручивания, тщательно изолируя место контакта.
- Холодные концы присоединяем к понижающей трансформаторной станции. Рекомендуется использовать установки SPB-40, ТМОБ-63, КТПТО-80 или их аналогов.
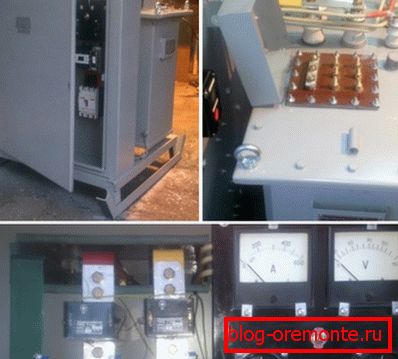
Note! Trial starts of the heating system before pouring concrete are not allowed, since this is highly likely to cause the conductors to burn out in air.
- To control the temperature we lay special tubes that will play the role of diagnostic wells.
- We perform pouring and vibration compaction of cement mortar, controlling the position and integrity of the conductors.
To reduce the cost of electricity for heating concrete to a predetermined temperature, experts recommend that you cover the foundation poured with foiled film. A layer of metallic spraying will play the role of a heat shield, reflecting infrared radiation and contributing to further strengthening the surface layer.
Recommendations for use
The warm-up process itself is implemented according to a three-stage scheme:
- Immediately after pouring, some time is given (up to two hours) to the primary setting. After that, the material is covered with insulating film and the transformer is started.
- The first stage is called preheating. The temperature of the solution gradually rises to 70 - 800C (depending on the project). At the same time, in order to avoid the formation of stress zones in concrete, the parameters of the current change gradually - so that the heating does not exceed 100With an hour.
- Next comes the longest second stage, in which isothermal heating of the cement mass occurs. At the same time, temperature conditions are controlled in the wells: the heating should not exceed 800C, otherwise the sintering of cement granules may begin.
- Processing is performed until the material gains 70% of the strength inherent in the project. Strength can be determined either by calculation or with the help of special tests (sometimes diamond drilling of holes in concrete is used for sampling).
- The third stage is cooling. The current parameters are changed so that the temperature of the concrete fell no faster than 4-50With an hour.

After this stage is completed, the “cold ends” are disconnected from the transformer and dismantled. Further durability takes place in natural conditions.
Conclusion
Information on how to warm up concrete with PNSV wire will be indispensable for anyone who plans to build a house in the winter. Of course, this system is quite an expense, but when there is not much choice, it is better to use the most efficient and affordable technology for heating concrete.
In any case, the above tips, as well as the video in this article contain information that is very valuable to the master, so you should take time to study it closely!