Concrete crown: structural features and the use of diamond,
Concrete drill bit (cup) is a special device used to drill holes in hard and extremely hard surfaces. These devices are not used by themselves, but with a hammer drill or other more powerful equipment.
Correctly selected crown for concrete determines the drilling efficiency no less than the main equipment. So, what and how to drill concrete products?

Basic classification
Crowns for drilling holes in reinforced concrete structures and products are available in various designs. The selection of a particular modification of the cutting tool is determined by such factors as the type and degree of hardness of the surfaces to be machined, the diameter of the hole, the type of drilling equipment, etc.

Modern crown for concrete, in accordance with the method of drilling, is available in two types:
- modifications for percussion drilling;
- modifications for hammerless drilling.
In accordance with the design features, the cutting tool is divided into the following categories:
- Toothed crown (carbide) - used for percussion drilling. The device is equipped with a cutting edge consisting of soldered carbide teeth. A shank is used to attach to the tool - SDS, SDS + and SDS max.

This kind of cutting tool is used when working with manual drills. The diameter of the holes when working with crowns of this type ranges from 20 to 100 mm.
Among the disadvantages of a toothed cutting tool should be noted the intensive wear of the edge and, as a consequence, the decrease in drilling efficiency. Moreover, in a collision with reinforcement, the edge becomes unusable without the possibility of subsequent recovery.
Another drawback of such tools can be considered an increased shock load on the treated surface, which adversely affects both the condition of the crown and the state of concrete structures.
- Diamond crown - This is a more technological and progressive device suitable for drilling by the non-impact method. The cutting edge, in this case, does not have metal teeth, since they are replaced by sputtering of corundum or diamond chips.

The main advantage of this device is the ability to effectively process reinforced concrete structures. The crown with a diamond coating significantly expands the possibilities of drilling, since the diameter of the holes in this case varies between 12-650 mm.
In addition to a large selection of diameters used, it should be noted that the use of crowns of this type allows drilling to a depth of 1.5 meters.
Devices with a cutting diameter of up to 100 mm have a standard SDS shank for installation in the punch. Such crowns are used without the mandatory use of liquid cooling.
- Diamond crown standard KS used for processing high-strength concrete and other materials with similar characteristics.

This tool has a cutting edge coated with polycrystalline diamonds. The coating is characterized by a special spraying technology, which makes the operation of the device especially long-term.
Such devices are used mainly with large-sized drilling equipment, not intended for manual operation.
Hammer drill tool

The modern concrete crown is a cylindrical device equipped with a connecting element (shank) for fixed installation in impact drills or rotary hammers of the SDS, SDS + and SDS max systems.
Such cups are manufactured using highly durable metal alloys that are resistant to elevated temperatures and to long-term impact. The working edge of these devices is equipped with defective teeth or other particularly strong alloys.
The cup, depending on the modification, can be equipped with a centering drill, which greatly simplifies the use of the tool.
Due to the special design of the cup and shank, an optimum transfer of force to the cutting edge is ensured. As a result, the crown at high speed, without application of excessive force, enters not only the silicate brick, but also the brickwork and concrete.
Diamond coated crowns - we drill stone with stone
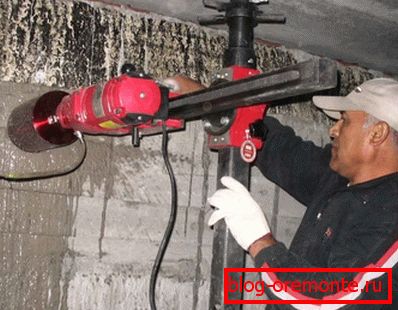
As already mentioned, diamond crowns are one of the most promising solutions for drilling holes of small and large diameter in materials with increased hardness. Using such devices, you can easily perform mechanical processing of reinforced concrete, masonry, natural stone, not to mention the light porous or cellular concrete that is popular today.
The main difference of this device from ordinary drills and drills is that only a thin edge contacts the surface of the material being processed. This difference allows not only to significantly increase the intensity of drilling, but also to minimize the destruction of the cut along the edges of the hole. Moreover, less contact between the cutting and machined edges turns into less noise and dust.
The history of the use of crowns for the treatment of solid surfaces has more than a decade. But, until recently, this equipment was used exclusively for the needs of the mining industry. Recently, such equipment began to be used during construction and repair and finishing works in buildings for residential, public and industrial use.
The main area of application of diamond-coated cutting tools is the laying of plumbing, gas and other utilities, as well as the cutting out of underside and other technological recesses.
Construction features of diamond crowns

The modern crown with a diamond dusting outwardly practically does not differ from similar devices entirely made of steel. In fact, this is the same cylinder, equipped with a connecting element (shank), designed to be fixed in the fixing element of the drilling equipment.
If on all-steel cylinders the cutting edge is an even metal cut with soldered metal hard alloy teeth, then in this case everything is somewhat different. Along the cutting edges of diamond crowns, not separate teeth are soldered, but wider segments with diamond or corundum sputtering.
There is a separate category of such devices in which individual segments are not soldered, and spraying is carried out continuously across the cutting edge. The tool with continuous ring spraying is used not so much for working with concrete, but for more subtle and neat work, such as for example, drilling ceramic tiles and tiles.
Of course, a hard-alloy crown on concrete is an order of magnitude cheaper than a diamond-coated counterpart. But the price of a diamond tool is justified by higher productivity. In addition, due to a longer resource, diamond tools are more economical by 60-80% compared to hard-alloy counterparts.
Important: With wear and tear, the cutting edge segments can be replaced with new segments, which will save money on the purchase of a new crown.
Service life of diamond crowns

How to increase the life of the crown with your own hands, without compromising the intensity of drilling?
First of all, to prevent wear of the tool allows water cooling of the cutting part.
In the process of drilling, the segments are heated to critical temperatures, as a result they can be unsoldered. To prevent this from happening, and so that the cup does not become unusable, the cutting elements should be cooled with running water during operation.
In addition to reducing the temperature, the running water allows for more efficient removal of the spent sludge. As it cools, polluted water must be collected with a special vacuum cleaner.
Important: If for one reason or another it is impossible to provide uninterrupted supply of water for edge cooling, it is advisable to use “cups” adapted for dry cutting.
To significantly extend the resource of the crown, you can correctly select the type of segments. In this case, the cutting edge will not be erased any longer, as a result, the segments will not need to be replaced, and especially you will not have to think about purchasing a new cup assembly.
Important: If you plan to work with reinforced concrete surfaces, it is advisable to use a “cup” coated with a soft bundle of diamonds. If you are drilling conventional high-quality concrete, the best solution would be the edge coated with a hard bundle of diamonds.
Use of carbide crowns
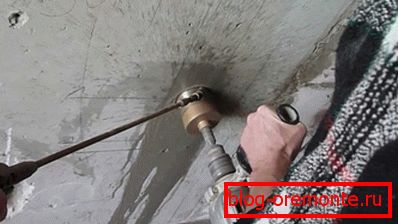
Consider how to use the crown for concrete if there is a punch. If you have an SDS, SDS + or SDS max perforator, you can purchase a carbide cup that will be enough for drilling holes with a diameter from 50 to 450 mm.
Going to the store for the cutting tool, select it, in accordance with the power of the punch and the type of connecting element. As a rule, crowns with a diameter of up to 250 mm can be placed on modifications with a capacity up to 1 kW.
The larger dimensions of the concrete crown are designed for more powerful equipment.
Important: Despite the fact that there are adapters on sale that allow large-diameter cups to be installed on low-powered drills, it is not recommended to use such tools, as the tool may not withstand excessive load and fail.
- When we start drilling, we are convinced that we face ordinary concrete without hidden reinforcement.
- Next, insert the shank for the concrete crown into the tool holder.
- If the cup is equipped with a centering drill, we attach it to the surface, if there is no drill, we lean directly on the cutting edge.
- While the cup does not go deep into the surface and does not get the right direction, it is not recommended to apply excessive physical force.
- Starting drilling, it is advisable to attract an assistant who will hold the vacuum cleaner hose, thus it will be possible to ensure effective dust removal.
- When working with a crown, do not periodically pull it out of the hole, as when working with a conventional drill. We deepen the cup to the very end.
- If the hole is through, the concrete will be inside the cup. Otherwise, the cup will be empty, and the hole will have to be further developed, freeing it from concrete.
Important: For drilling thick walls or floors, an extension crown can be used for concrete.
Application of diamond crowns

Instructions for the use of diamond crowns differs from the use of carbide cups. A special feature is the use of technically complex devices, which, unlike a perforator, allow drilling without vibration effects.
Moreover, the device is fixed on the treated surface, which allows making holes positioned in the desired direction. The fixed tool greatly facilitates the work, as the worker needs to move the equipment in the course of drilling, but does not need to hold it. Thus, high cutting accuracy is achieved, which other devices are not capable of providing.
Conclusion
Now you know what types of crowns are used for mechanical processing of concrete structures and structures. Moreover, now you have a general idea of drilling technology with this tool.
If you have any questions that require explanation, watch the video in this article.