Composition of lightweight aggregate: proportions and
The composition of expanded clay used in construction is governed by the requirements of GOST 6133-99, which describes the technical conditions for the production of wall stones. To obtain high-quality products, it is necessary not only to adhere to the proportions indicated in the document, but also to observe the optimal parameters of the flow of all technological processes.
And yet it is the quality and ratio of ingredients that is decisive. Therefore, this issue needs to be given the closest attention, both at the production planning stage and in the control of work.

Blend components
Binder
Cement is injected into the claydite mixture as a binder.
The requirements for it are fairly strict:
- Brand - not lower than M400. The use of low-grade binder can lead to the formation of inhomogeneities in the thickness of the material and its destruction under its own weight.
- Use of cement with pozzolan additives should be coordinated with an experienced technologist.. This is due to the fact that pozzolanic additives, when reacting with dust, which is contained in the expanded clay, form unstable complexes, which can reduce the moisture resistance of the finished material.
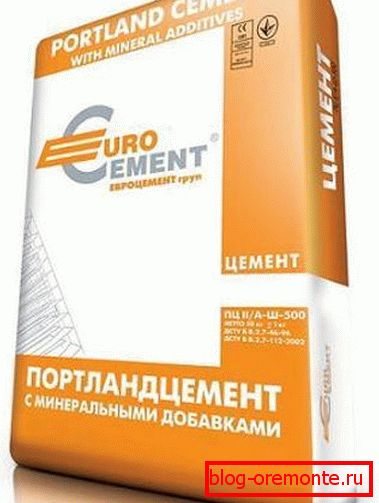
Note! It is also undesirable to use plasticizing agents, since they can reduce the strength of concrete blocks during the initial solidification stage.
- If heat treatment of claydite-concrete modules is planned, then a small amount of alite cements including silicates can be added to the solution.. In this case, the polymerization of the material during heating will be more active.
The cement content in the composition is directly proportional to its strength. However, with an increase in the proportion of the binder, the insulating capacity decreases, therefore, claydite-concrete with different performance characteristics is used for various purposes.
Water requirements
As for water, the instruction recommends using the same liquid that is used for mixing ordinary concrete.
It is characterized by such requirements:
- Lack of solid inclusions.
- Отсутствие загрязнений органическими веществами, mаслами, нефтепродуктами.
- pH not less than 4.
- The sulfate content is not more than 1% by volume.

In principle, in most cases either drinking or process water is used as a solvent. The use of open reservoirs is also allowed as a source, but in this case the liquid must undergo primary purification from impurities and mechanical impurities.
Tip! Seawater should not be used for the preparation of claydite-concrete solution: high salt content will necessarily lead to the formation of whitish stains on the surface of the building stone.
Fillers and additives
However, the main component, which determines the entire composition of the mixture for claydite-concrete blocks, is the aggregate. As this ingredient, either claydite itself or claydite sand obtained by crushing is used.

Expanded clay is one of the most popular materials used in the manufacture of building blocks with high thermal performance.
The following is typical for him:
- Porosity - up to 70% of the total volume of the material.
- The average pore diameter is 1 mm.
- According to the form, claydite is divided into gravel (rounded granules with melted surface) and crushed stone (granules of irregular shape, open pores are visible on the surface).
- The material used to fill cellular concrete must have a frost resistance of at least 15 cycles. Acceptable water absorption varies from 25% (for grades 400 and less) to 15% (for structural claydite-concrete 700-800).
- In industrial production, claydite particles ranging in size from 1.2 to 5 mm can be used.
Expanded clay is usually obtained by grinding gravel or crushed stone in special mills. It should be noted that this material is characterized by a large adsorption of water and cement, which leads to some decrease in the quality of the solution.
Note! You can also produce sand by burning the original clay raw materials in kilns. For such a filler, excessive water absorption will not be relevant. However, its price due to the cost of production is somewhat higher, because it is used infrequently.
Production technique
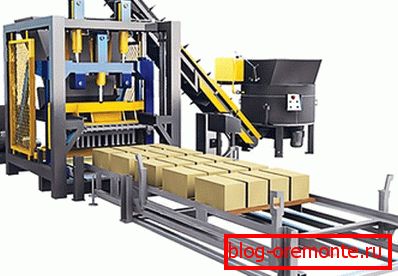
With the above ingredients and learning techniques, you can make the material yourself. Naturally, in this case, the quality largely depends on the exact calculation of the proportions. Examples of the composition of the mixtures are given in the table below:
Ingredients | The density of expanded clay, kg / m3 | |||
1000 | 1500 | 1600 | 1700 | |
Cement M400, kg | 250 | 430 | 400 | 380 |
Expanded clay 700 kg / m3, m3 | 1,1 | 0,8 | 0,72 | 0,62 |
Sand kg | - | 420 | 640 | 830 |
Water, l | 140 | 140 | 140 | 140 |
Note! Figures may vary when using cement of other grades or aggregates that differ in density
The very method of making keramsit concrete is quite simple:
- In the mixer for cement we pour the required volume of water. It is better to take a little less than you need according to the instructions so that the solution does not turn out to be too liquid.
- We fill up the cement and sand in the required proportions, constantly mixing the composition.
- Next, in parts, we enter claydite into the solution, distributing it evenly throughout the volume.
- As a result, we should get a fairly homogeneous mass, the consistency of a batter.
- If the fluidity of the solution is insufficient, you can add some water and re-mix it.

Then you can either immediately pour the material into the formwork for concrete products, or fill out forms with them for the manufacture of building blocks. In the second case, we need to dry the products thoroughly, removing all moisture from them and ensuring durability. This is best done in special drying chambers.

Conclusion
The composition of expanded clay in the volume fractions of each component given in the article is, of course, not the final version. For the manufacture of materials that differ in density and thermal conductivity, you can use other ratios of cement, sand and aggregate. However, the general scheme of production remains unchanged, as evidenced by the video in this article.