Cement concrete: material properties and characteristics
Cement concrete - one of the most common building materials, which is used for the production of concrete products, as well as for housing and road construction. In many respects, cement concrete roads are superior to asphalt ones, which was the reason for the increased attention to this material from the engineers and designers of transport routes.

Cement based concrete
Properties and specifications

Concrete is a stone material of artificial origin, which is used in the construction and manufacture of products from reinforced concrete. It is obtained by the formation and subsequent hardening of a specially selected mixture of components, including a binder (cement, gypsum, bitumen, etc.), small and large fillers, water, and special targeted additives.
The classification of concrete is made according to GOST 25192-2012, GOST 25192-82 and GOST 7473-2010 according to various indicators: bulk density, main purpose, type of binder, type of fillers, hardening conditions and structure.
Here are the main types of concrete:
- By volume - especially heavy (with a density of more than 2500 kg / cub. M), heavy (from 2200 to 2500 kg / cub. M), lightweight (1800 - 2200 kg / cub. M), light (500 - 1800 kg / cub. M) and particularly light (with a density of less than 500 kg / cubic meter);
- By type of binder component - silicate, gypsum, cement, slag alkaline, polymer, asphalt;
- According to the main purpose - the usual used for the construction of industrial and civil facilities, special, including hydraulic, thermal insulation, road, decorative, heat-resistant, acid-resistant, radiation-protective;
- By type of fillers concretes are divided into mortars on dense, porous and special fillers;
- According to the conditions of hardening There are materials of natural hardening, hardening under conditions of heat-humidity treatment at atmospheric pressure and autoclave hardening;
- By structure produce products of cellular, large-pore, porous and dense structure.

Note! Cement concrete mix for road surfaces after solidification gives heavy dense cement concrete of natural hardening, special purpose on dense fillers.
Benefits for road construction
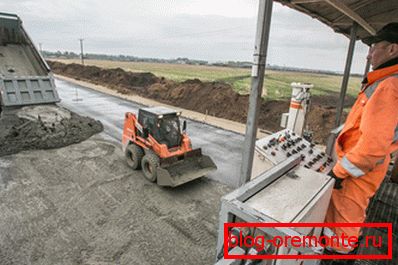
Cement concrete road pavements differ from traditional asphalt by a number of qualities. Moreover, these qualities are very essential, on which depends not only the beauty and comfort of the roadway, but also its reliability, safety and durability.
Compared with asphalt concrete, cement have the following advantages:
- Higher strength. Cement mixtures give a stone that can withstand higher compressive, tensile and flexural loads in tension, which has a positive effect on the operational features of the road surface;
- Resistance to elevated and high temperaturesarising from the infrared radiation of the Sun, as well as from friction of tires and exposure to hot exhaust gases, and in the case of runways of airfields - the effects of jet engines. Unlike asphalt, cement concrete does not melt or burn;
- Resistance to abrasion due to traffic. It has been established that during the year the cement sheet is washed about 1 mm, which is relatively small;
- Durability. The design life of the roads of this material is about 30 years, and the real can easily reach 50 or more;
- Resistance to aggressive chemical environments and oil products. It is also an important quality indicator for pavements that are constantly in contact with the combustion products of gasoline and diesel fuel, water, salts and their solutions and other chemicals.

Of course, there are disadvantages of the use of cement concrete in road construction. This is a higher price of the material, the probability of swelling and cracking of the upper layer, as well as the need to arrange longitudinal and transverse deformation seams in cement concrete, where labor-intensive cutting of reinforced concrete with diamond circles and diamond drilling of holes in concrete, which are made by special machines, is assumed.

Note! Concrete pavement of roads is exposed to many factors of wear, so the instruction places quite stringent requirements on the quality of the components and the formulation of the mixture, as well as on the conditions of preparation, storage and transportation of the solution.
Requirements

Given the special operating conditions and increased specific wear of the material, cement concrete for road surfaces should be made in accordance with a number of requirements. These are, first of all, the requirements for the component composition of the mixture (also learn how the lag is fixed to the concrete floor).
Cement for such a solution should refer to the type of Portland cement. The mark is allowed not lower than M400, and for bases of multilayer coatings - not lower than M300.
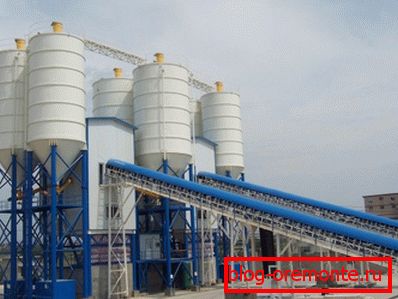
In this case, the frost resistance mark is standardized, it should not be lower than F 150, and for bases - not lower than F 50. These figures show the number of freezing / thawing cycles in the presence of chloride salts.
Another important characteristic affecting the mobility and strength of concrete is the water / cement ratio or W / C. Theoretically, mixing the concrete is V / C = 0.2, but in practice such a solution is too rigid and immobile, and its laying is impossible.
For a road solution, B / C is normalized within the following limits: no more than 0.5 for the upper layers, no more than 0.6 for the lower layers, and no more than 0.75 for the bases.
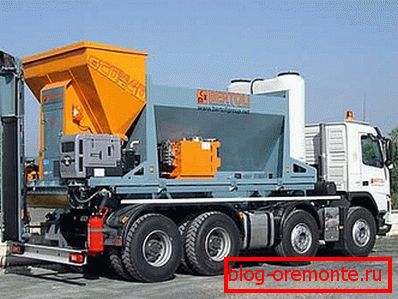
The composition of the fillers must also comply with the rules and regulations. Sand is allowed natural large, medium and fine-grained, crushed stone - the optimal particle size with the amount of impurities of not more than 1%. Fractional composition is accepted up to 40 mm - for a single-layer coating or a lower layer of a two-layer, up to 20 mm - for an upper layer of a two-layer coating.
Concrete is prepared on concrete mixers of cyclic type of action or on mobile installations of continuous action, and is laid using a set of concrete-laying and concrete-finishing machines, as well as machines for cutting shrinkable joints.
Conclusion
Cement concrete is an excellent raw material for the construction of modern highways, runways and highways. The material is superior to traditional asphalt in a number of important indicators, and the video in this article demonstrates the process of laying the solution on the road (find out here what is the modulus of elasticity of concrete).